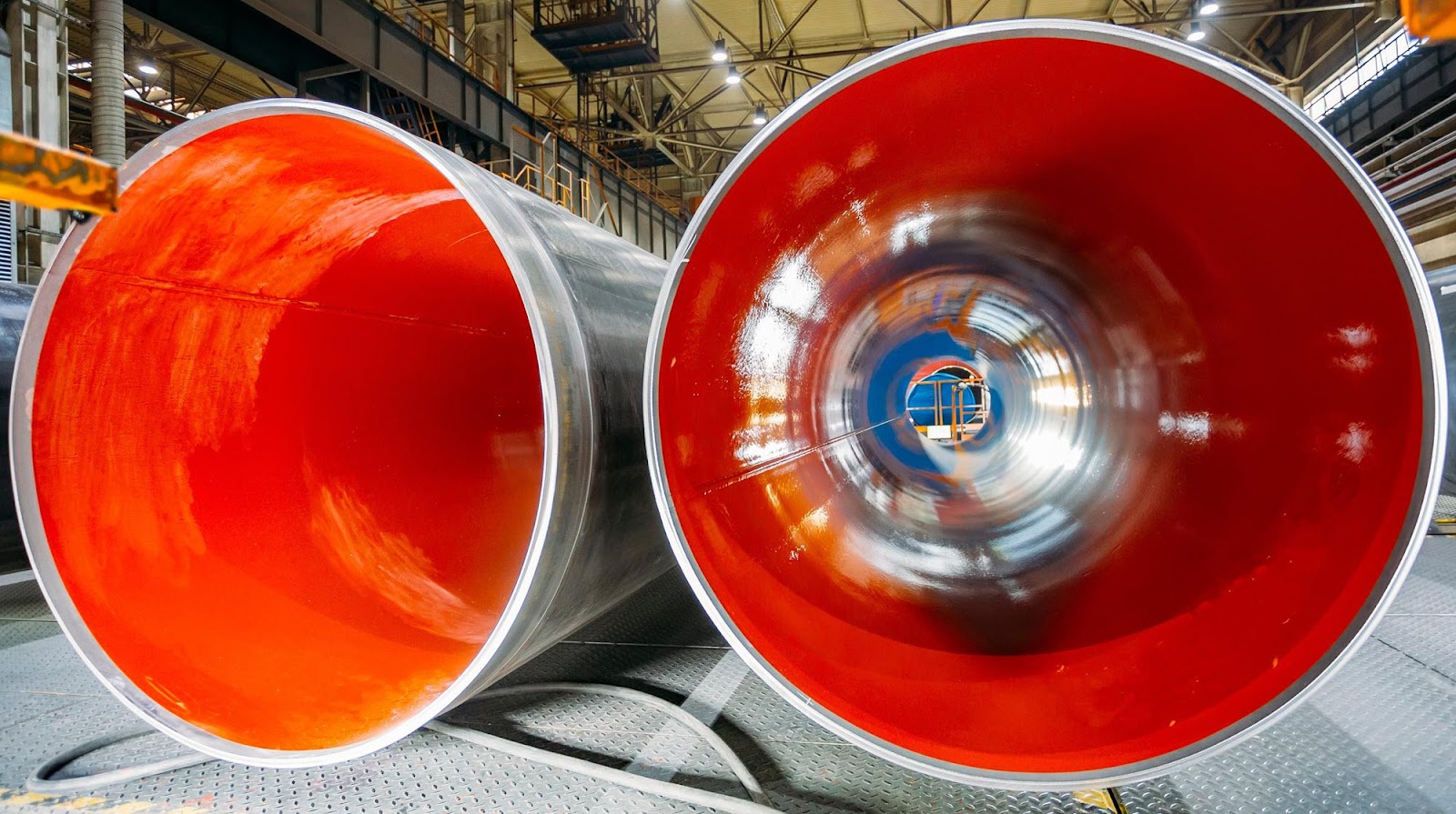
Protective measures for pipelines have played a role in advancing infrastructure over the years; conventional coatings such as epoxy and polyurea have been at the forefront for many years. Nevertheless, polyurea has started to gain prominence in the market due to its superior qualities that surpass those of older methods. Ranging from application to increased longevity, polyurea is demonstrating itself as the next frontier in pipeline protection, excellently outshining conventional coatings in critical aspects that significantly impact long-term effectiveness.
Polyurea coatings are notable for their flexibility and seamless bonding with materials,, which makes them a popular choice in pipeline projects that regularly face challenges like moisture exposure and chemical wear and tear. It is vital to have a coating that can endure strains effectively in such environments. Unlike coatings like epoxy, which tend to become brittle over time and develop cracks, exposing the pipeline to corrosion risks, polyethylene's flexibility enables it to adjust with the pipeline's movements due to temperature changes, thus decreasing the chances of failure occurring.
polyurea coatings offer a perk with their quick curing time as compared to traditional coatings, that can take hours or days to fully cure and potentially slow down pipeline construction or repairs processes. Unlike coatings with lengthy curing times, polyurea cures in a matter of seconds, speeding up the project timeline and cutting down on downtime, which is crucial, for large scale pipeline coating projects as it helps minimize costs and keep the work flowing smoothly without unnecessary interruptions.
Coatings can shield against corrosion. Polyurea goes beyond by creating a waterproof barrier that sticks tightly to the pipeline's surface.This seamless application blocks water and chemicals from seeping through the coating to reach the metal underneath.This added layer of protection is crucial for maintaining the integrity of pipelines in challenging environments exposed to conditions, over time.
Polyurea coatings have become more popular than options because they can withstand mechanical damage well. Pipelines often face impact and friction during installation or upkeep from materials and tools.The flexibility of polyurea allows it to absorb these impacts without breaking or peeling off. This helps protect the pipeline from both, inside and outside threats.In contrast epoxy and other rigid coatings may struggle under circumstances, resulting in vulnerable areas that need expensive fixes.
Polyurea has mechanical properties and also provides exceptional chemical resistance that sets them apart from other coating options available in the market today! When it comes to pipelines handling materials that can wear down traditional coatings over time; polyurea stand out for their ability to withstand a wide array of substances – from oil and gas to industrial chemicals and even wastewater! This makes polyurea a go to choice across industries due to their adaptability and effectiveness in protecting pipelines carrying different materials without the hassle of using specialized coatings for each type of liquid being transported.
Polyurea excels in withstanding temperatures compared to standard coatings when it comes to temperature resistance capabilities.Ranging temperatures, such as freezing cold or intense heat can cause traditional coatings to deteriorate easily; however polyurea exhibit stability over a broad temperature spectrum without compromising their protective characteristics by becoming fragile or flexible.This reliability makes polyurea a dependable choice for pipelines situated in geographical areas, like Arctic zones or desert environments.
When it comes to coatings traditionally used in the industry they usually need surface prep work and multiple coats to provide good protection.. In contrast, polyureaa requires one coat with minimal prep work. This not only makes the application faster but also increases the likelihood of mistakes that commonly happen with multi-step coating processes.. Additionallyy polyureaas capability to adhere directly to surfaces like steel and concrete adds to its attractiveness making it convenient for use, in challenging settings.
Less talked about but equally important in pipeline coating is the impact of the materials utilized. Polyurea coatings with VOC content are considered more eco-friendly than conventional choices.Reducing the release of chemicals during application not only aids pipeline projects in complying with stricter environmental rules but also guarantees a safer working environment for those involved in applying the coatings.
Many websites highlight the benefits of polyurea without delving into the cost effectiveness that comes from their durability and reduced maintenance requirements. Unlike coatings that demand regular inspections and touch ups due to their proneness to cracking and peeling issues Polyurea offer lasting protection that minimizes the necessity for ongoing maintenance thus decreasing the overall expenses associated with safeguarding pipelines. For enterprises seeking to optimize their infrastructure investments the allure of polyurea lies in their ability to provide a cost solution, with long term benefits.
Pipeline protection in the future is moving more towards polyurea as companies realize the advantages they have over methods.They are quick to apply and offer durability and environmental benefits compared to other options.This makes polyurea a top choice for both setting up pipelines and carrying out maintenance projects.Companies such as ArmorThane that focus on polyurea are, at the forefront of offering solutions that cater to the changing demands of the pipeline sector.
In summary polyurea coatings have emerged as the leading solution for safeguarding pipelines and offering pipeline rehab thanks to their flexibility, drying time and resilience against both physical and chemical threats. As businesses strive to enhance pipeline protection methods the superior qualities of polyurea over coatings make it the preferred option moving forward. With improvements, in polyurea formulation and application techniques it is probable that its prevalence will expand further as more organizations embrace this cutting edge protective solution.